What is Porosity in Welding: Common Sources and Reliable Remedies
What is Porosity in Welding: Common Sources and Reliable Remedies
Blog Article
The Science Behind Porosity: A Comprehensive Guide for Welders and Fabricators
Recognizing the detailed devices behind porosity in welding is vital for welders and makers making every effort for flawless workmanship. From the composition of the base materials to the details of the welding process itself, a multitude of variables conspire to either worsen or alleviate the visibility of porosity.
Recognizing Porosity in Welding
FIRST SENTENCE:
Examination of porosity in welding discloses crucial understandings into the stability and quality of the weld joint. Porosity, defined by the visibility of cavities or voids within the weld metal, is a common concern in welding procedures. These voids, if not effectively resolved, can compromise the structural integrity and mechanical homes of the weld, causing possible failures in the ended up item.

To discover and measure porosity, non-destructive testing methods such as ultrasonic screening or X-ray examination are commonly used. These strategies permit for the recognition of inner defects without endangering the stability of the weld. By assessing the dimension, form, and circulation of porosity within a weld, welders can make educated decisions to boost their welding processes and attain sounder weld joints.

Aspects Affecting Porosity Development
The incident of porosity in welding is affected by a myriad of factors, ranging from gas securing effectiveness to the details of welding criterion settings. Welding parameters, consisting of voltage, existing, take a trip rate, and electrode type, likewise influence porosity development. The welding technique utilized, such as gas metal arc welding (GMAW) or secured steel arc welding (SMAW), can influence porosity development due to variants in warm circulation and gas insurance coverage - What is Porosity.
Results of Porosity on Weld Quality
The visibility of porosity likewise weakens the weld's resistance to deterioration, as the caught air or gases within the gaps can respond with the surrounding environment, leading to destruction over time. Furthermore, porosity can hinder the weld's capacity to endure stress or influence, additional endangering the total high quality and reliability of the bonded structure. In important applications such as aerospace, vehicle, or structural building and constructions, where safety and longevity are vital, the detrimental impacts of porosity on weld quality can have severe repercussions, emphasizing the significance of decreasing porosity through appropriate welding strategies and procedures.
Techniques to Reduce Porosity
Furthermore, utilizing the ideal welding specifications, such as the right voltage, existing, and take a trip speed, is crucial in avoiding porosity. Maintaining a consistent arc length and angle throughout welding likewise assists minimize the probability of porosity.

Utilizing the appropriate welding strategy, such as back-stepping or utilizing a weaving movement, can also assist distribute warmth uniformly and lower the possibilities of porosity formation. By applying these techniques, welders can properly reduce porosity and generate premium bonded joints.
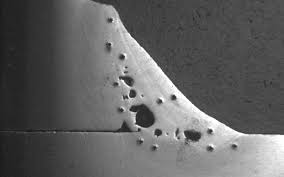
Advanced Solutions for Porosity Control
Implementing innovative innovations and innovative techniques plays a crucial role in accomplishing superior control over porosity web link in welding processes. Furthermore, using sophisticated welding strategies such as pulsed MIG welding or modified atmosphere welding can likewise assist minimize porosity issues.
One more innovative remedy Continued involves using sophisticated welding equipment. As an example, using tools with integrated features like waveform control and innovative power sources can enhance weld high quality and reduce porosity risks. The implementation of automated welding systems with exact control over specifications can substantially lessen porosity flaws.
In addition, including innovative surveillance and inspection innovations such as real-time X-ray imaging or automated ultrasonic testing can assist in identifying porosity early in the welding procedure, enabling prompt corrective activities. On the whole, incorporating these sophisticated services can significantly improve porosity control and boost the overall top quality of bonded elements.
Conclusion
In conclusion, recognizing the science behind porosity in welding is essential for welders and makers to create high-quality welds - What is Porosity. Advanced remedies for porosity control can even more boost the welding process and make sure a Continue strong and dependable weld.
Report this page